DP – 3
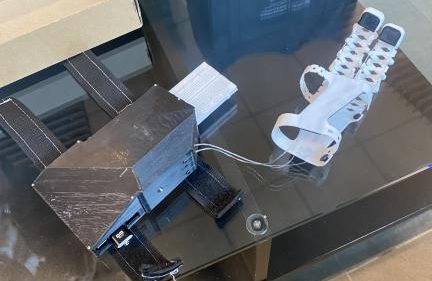
A Sense of Independence
(iBiomed Project 3)
👤 Background
Individuals with limited hand mobility due to nerve damage, joint issues, or general muscle weakness often face significant challenges in performing daily tasks and maintaining their independence. Conditions such as strokes, multiple sclerosis, or paralysis can lead to hand mobility limitations, hindering the ability to carry out everyday activities and impacting the overall quality of life
Identified Solution
❤️ Need
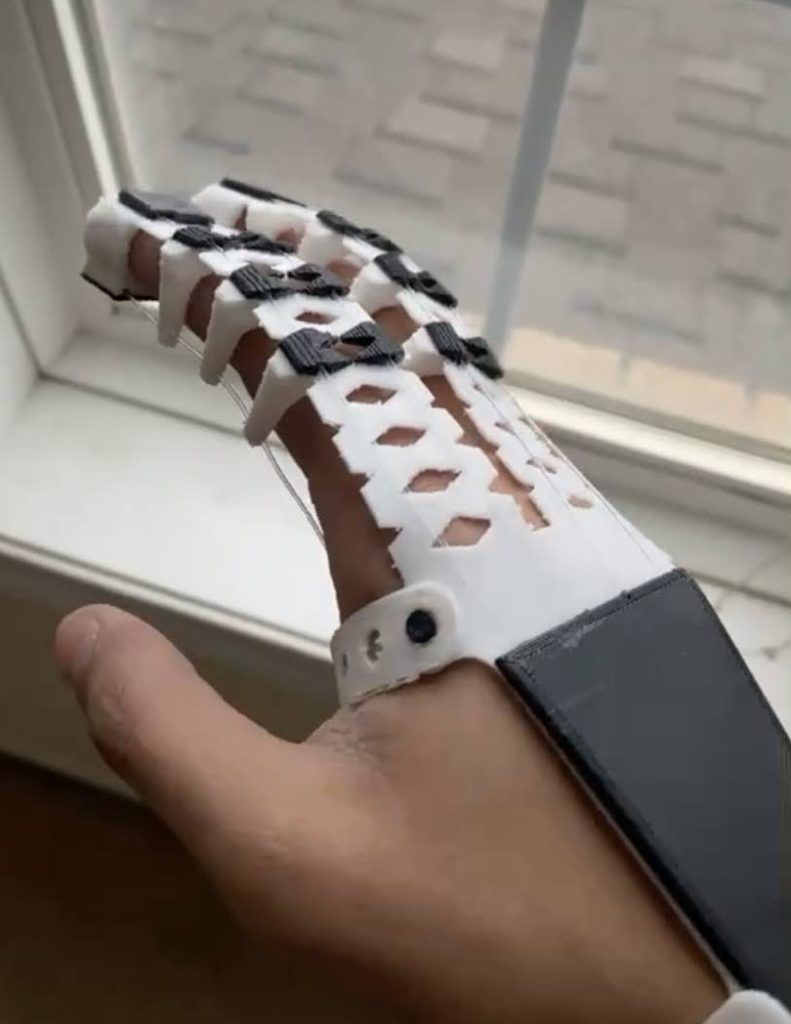
The EXO-FLEX is an assistive glove made for people with limited mobility in their hands. Its purpose is to provide extra gripping strength and stability to aid the user in their daily activities, improving their overall quality of life. The glove is designed to move the user’s 2nd and 3rd fingers by pulling strings attached to the front and back of the hand.
Design an affordable, adaptable, and portable assistive device that enables individuals with limited hand mobility to perform daily tasks independently, thereby enhancing their overall quality of life and promoting self-sufficiency.
🎯Objectives
- Should assist individuals with hand mobility impairments.
- Should improve the user’s ability to perform daily dexterity related tasks
- Should enhance the user’s quality of life and independence.
- Should be affordable and accessible for the target demographic
🚧 Constraints
- Must use limited budget and resources for prototype development.
- Must be completed within 1-2 month time for designing, testing, and refining.
- Must be in a form-factor which makes sense to the patients requirements,
- Must be durable and reliable during extended use.
🔑 Functions
- Provide mechanical assistance to augment the user’s grip strength and dexterity.
- Incorporate sensors and actuators to facilitate intuitive and responsive control.
- Design a comfortable, ergonomic fit that accommodates various hand sizes and shapes.
300$ to make
Can be further reduced to less than 50$ if we use an alternate processor such as an Arduino as a RaspberryPI which is the current device is more powerful than we need it to be.
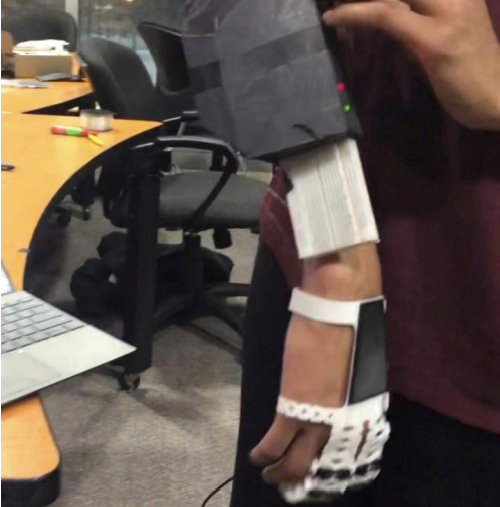
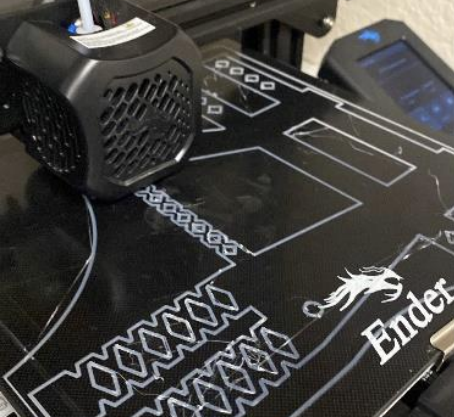
🧑 My Individual Contributions
- Utilized CAD towards creation and design of both hand component, housing component, mechanism, and final assembly on my personal 3D printer.
- As Project Manager, created a preliminary Gantt chart and weekly agendas to ensure project progress
- Assembly and Integration of EMG Sensors and Servo output to interact with mechanical device.
- Researched Material and Design verification using computer programs to optimize design strength as pictured below
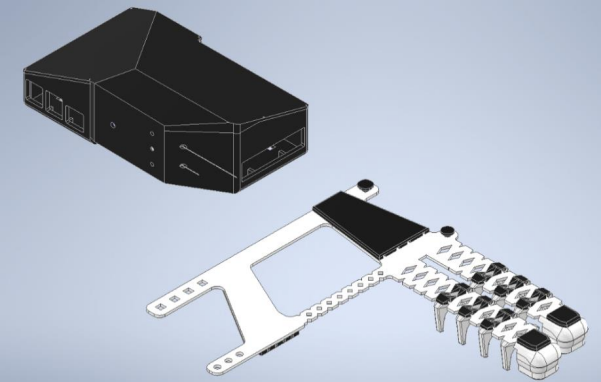
Contribution Images
🔨 Applied Skills
🧠 Soft Skills
- Collaboration
- Presentation skills
- Lateral thinking
- Project management
⚙️ Hard Skills
Autodesk Inventor
PowerPoint
Python
PrusaSlicer (3D Printing)
- 🛠️ Prototyping
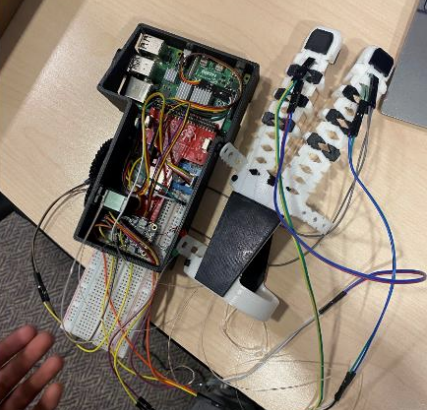
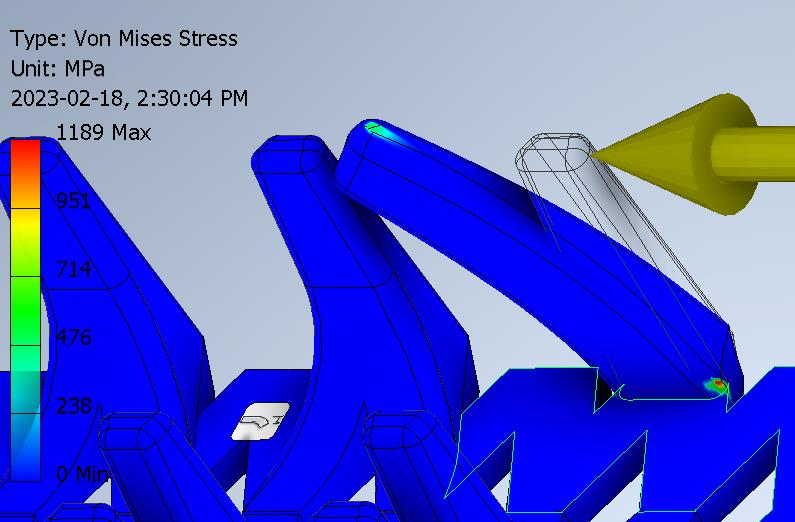
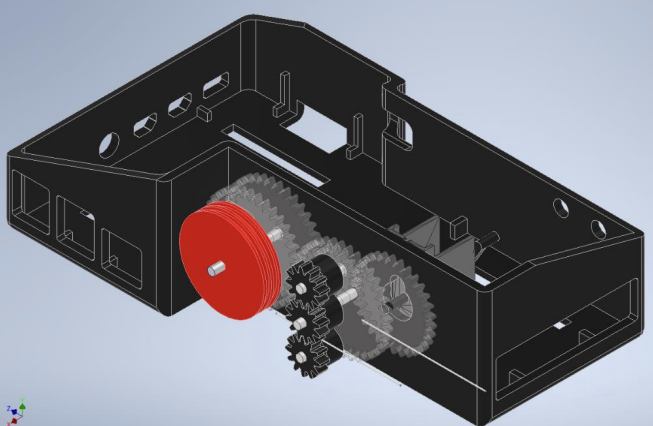
📐 Design Process
- After creating some general preliminary sketches for our solution we created a combined concept sketch with the opening/closing mechanism for the Exo-Flex
- Printed Exo-Flex Hand part completely with TPU flexible filament to wrap around you hand
- I tested around with various designs to optimize the wrist strap, one-piece assembly design for the accurate application. Approx. 15 different prototype iterations
- The group eventually implemented the code within the mechanism and tested to fix bugs and re-iterated the design to be more effective by using EMG,
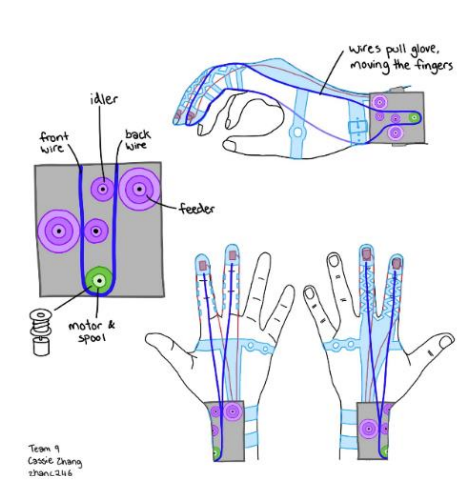
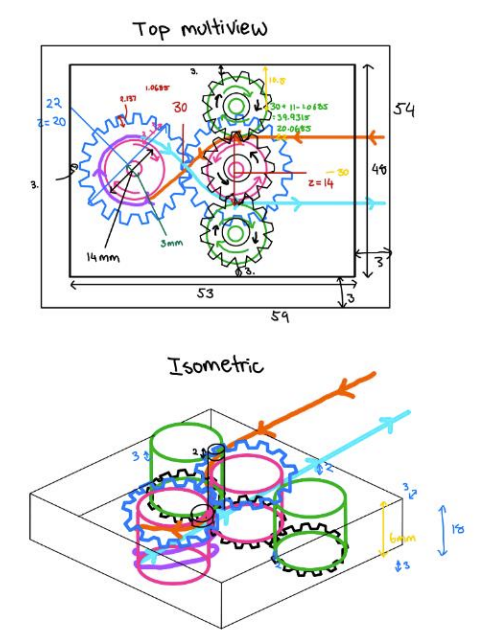
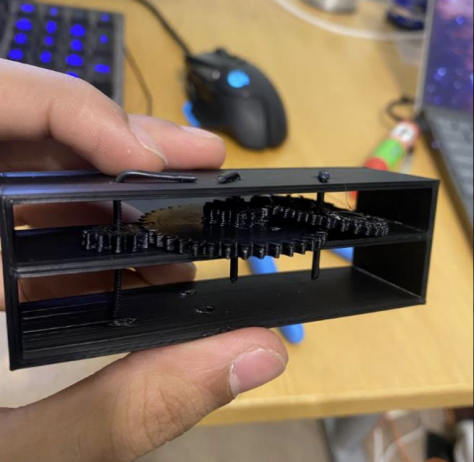
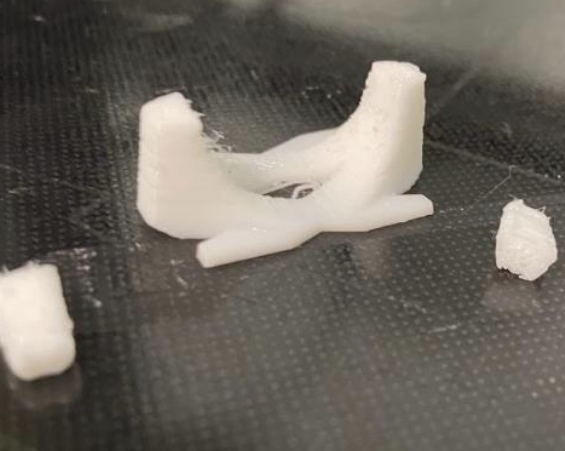
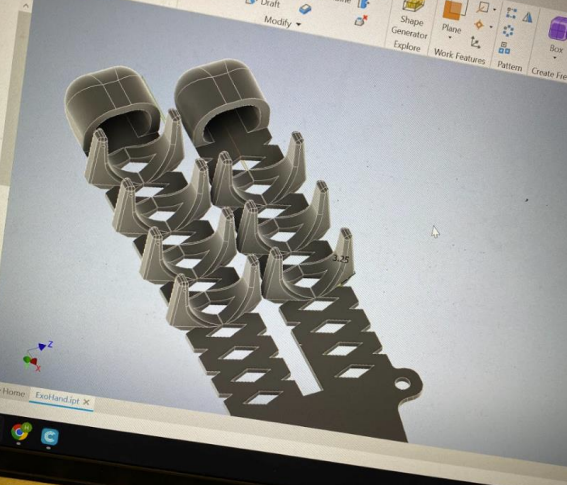
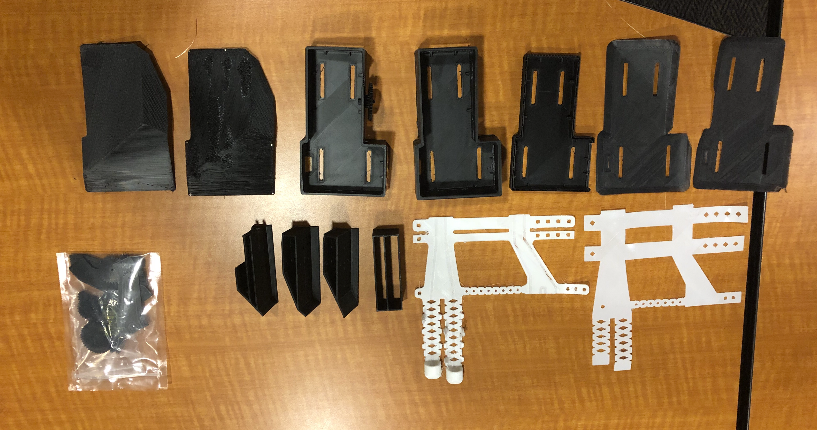
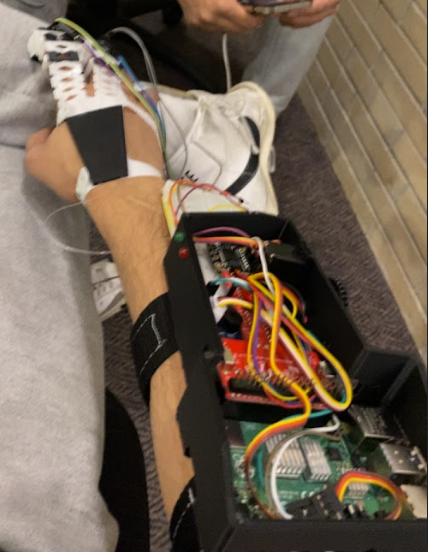
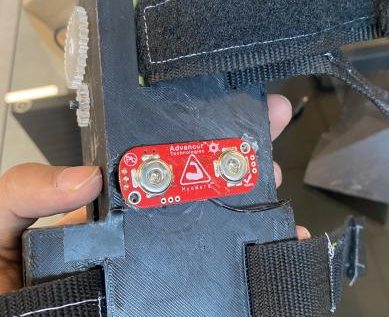
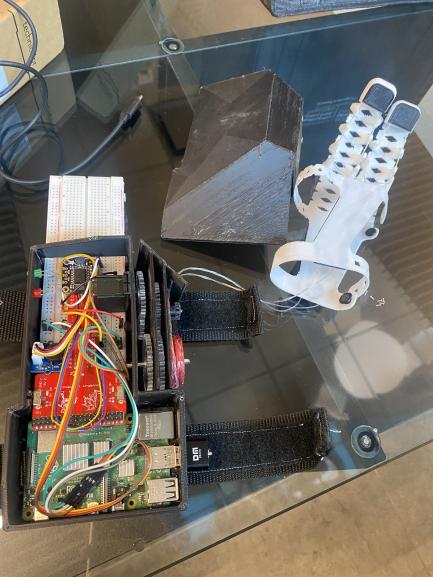
- ❌ Plastic 3D printed gears & axles were not strong enough to reliably pull the string with the mechanism
- ✅Replaced plastic with acrylic gears and and stronger axles resulting in a significantly more durable mechanism.
- ❌ Initial design for finger supports was not strong enough so it would easily break
- ✅Redesigned to be thicker and much more resistant to normal usage damage.
- ❌ Initial plan to incorporate touch sensors was impractical and and gave unreliable readings and led to a more narrow market
- ✅Discussed with potential clients (David) and re-imagined our product with a EMG sensor to be activated with muscle force rather than FSR.
Final Design
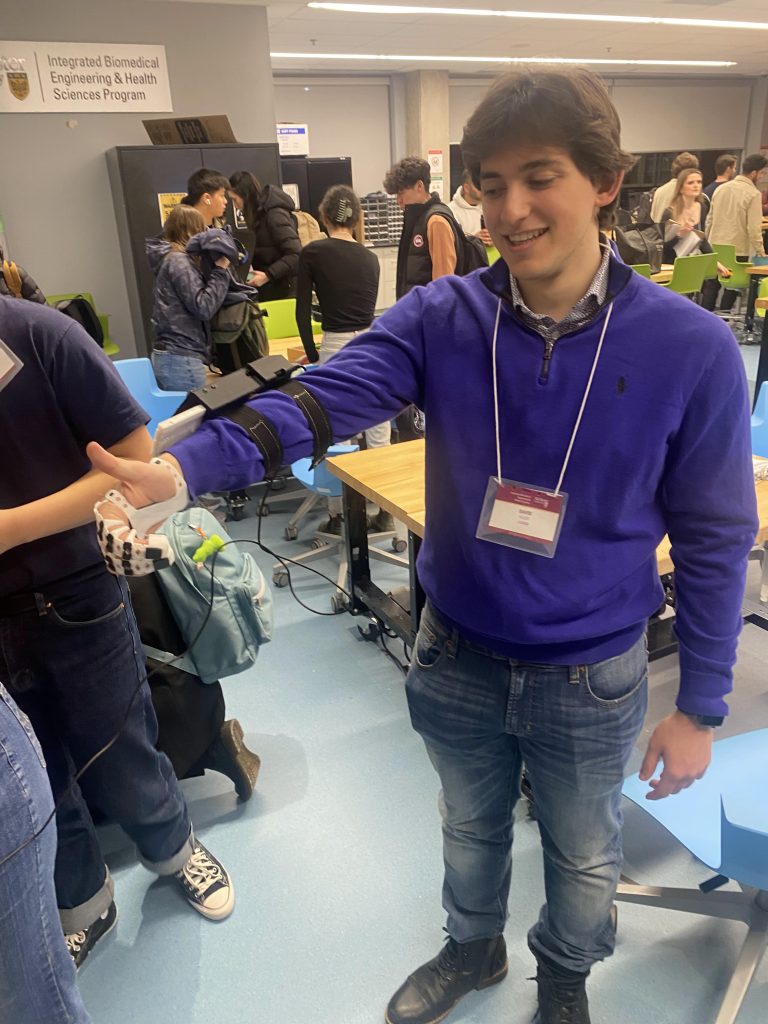
Expo. He was fitted him with the design and taught how to use it within just a few minutes.
Final Prototype
- The final prototype of the ExoFlex is an assistive glove designed for individuals with limited hand mobility.
- The glove is made of flexible material, allowing it to adjust to the user’s hand movements.
- The device is designed to provide extra gripping strength and stability by pulling strings and enabling users to perform daily activities with ease.
- Visual and auditory alerts are integrated into the design to improve the user interface and make the device easy to operate.
- The ExoFlex is an affordable, portable, and adaptable solution aimed at enhancing the overall quality of life for people with limited hand mobility.
Electronics
LEDs
Red – Indicates initiation of closing motion
Green – Visual indicator to show device is running.
Buzzer:
Indicates to user that Exo-Flex is at maximum flexion position.
Output device servo:
Controls the closing/opening motion of the hand through a mechanism although it is limited by 120 degree.
Input device EMF:
Detects muscle flexion/compression and is used to indicate speed/direction of intended movement from coded software
Personal Reflective Summary
Less guidance makes things more difficult than they may seem…
This design project presented me with a unique opportunity to experience the challenges and rewards of open-ended problem-solving. While on one hand I was appreciative of this opportunity as a group we also found it very difficult to come up with a single demographic and focusing a solution to a problem. This is why during the initial phase we spent a lot of time questioning whether our device is actually needed by the target demographic of individuals with dexterity issues. By creating the PUGH MATRIX it really helped us asses our ideas and that definitely something I plan to incorporate in my future projects. Furthermore another key lesson I learned was the importance of prioritizing functionality and feasibility over complexity. At one point, our team considered integrating control of all 5 fingers to enhance the user’s experience. However, this addition would have significantly increased the complexity and cost of the ExoFlex prototype. As I reflected on this decision, our group really questioned if the added functionality was truly necessary for our target demographic. We weighed the potential benefits against the constraints of time, budget, and technical feasibility. Ultimately, we decided to focus on only the two main fingers in order to refine the core features of the ExoFlex to ensure a functional, reliable, and user-friendly solution. This really makes me question if it would even be possible to complete the project if we tried to use all 5 fingers. This experience taught me to critically evaluate what is actually necessary and practical for the problem being solved. I think this is really important for future projects as overcomplicating ideas can result in a lot of time and resources wasted. This project has helped me grow as an engineer and innovator, and I look forward to applying these lessons to future endeavors.
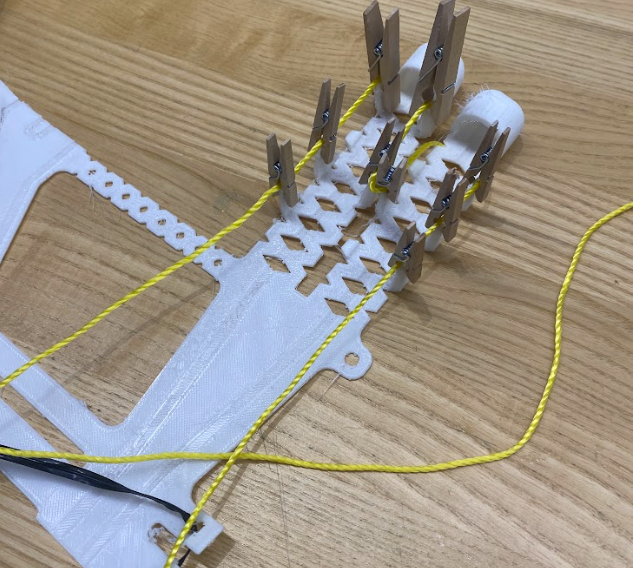
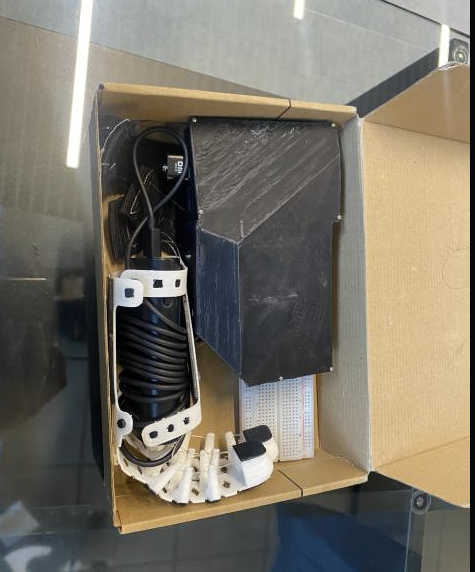
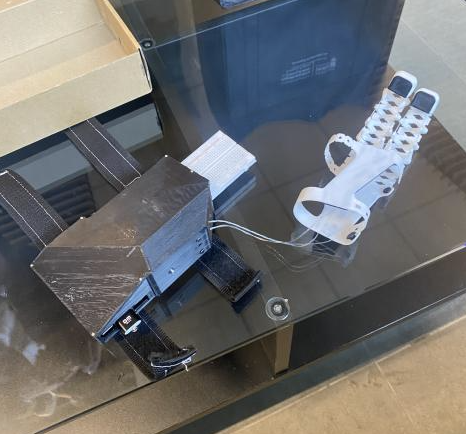